manual forklift jack
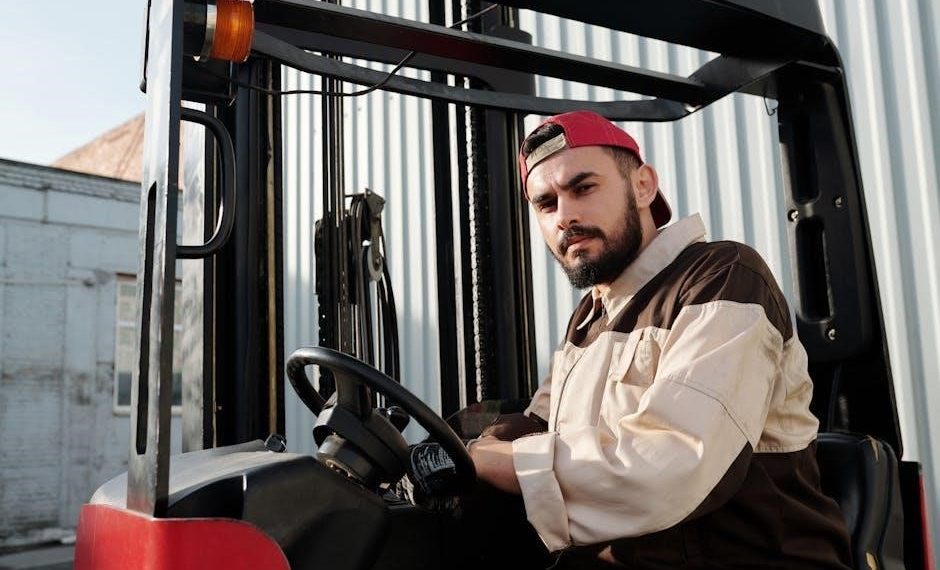
manual forklift jack
A manual forklift jack is a essential tool for lifting and moving heavy loads in various industrial settings. It provides efficient, safe, and precise material handling solutions.
1.1 Definition and Purpose
A manual forklift jack is a portable, self-contained lifting device designed to elevate heavy loads, typically in industrial or warehouse settings. It operates using a hydraulic or mechanical system, requiring manual effort to lift and lower loads. The primary purpose of a manual forklift jack is to safely and efficiently handle materials, reducing the need for manual labor and minimizing the risk of workplace accidents. Unlike larger forklifts, manual jacks are compact, cost-effective, and ideal for smaller-scale operations. They are essential tools for businesses that require frequent lifting of pallets, equipment, or supplies. Their versatility and ease of use make them a cornerstone in many industries, ensuring smooth workflow and operational efficiency.
1.2 Comparison with Other Lifting Tools
Manual forklift jacks are often compared to other lifting tools like electric forklifts and overhead cranes. Unlike electric forklifts, manual jacks are more cost-effective and require less maintenance, making them ideal for smaller operations. They are also more portable and can be used in spaces where larger equipment cannot fit. Compared to overhead cranes, manual jacks offer greater flexibility and do not require permanent installation, making them suitable for temporary or variable lifting needs. While they may lack the lifting capacity of larger machines, their simplicity and ease of use provide significant advantages in specific scenarios. Additionally, manual jacks are quieter and produce no emissions, making them environmentally friendly options for indoor use. Overall, manual forklift jacks strike a balance between affordability, portability, and functionality, catering to unique operational requirements.
Safety Guidelines for Manual Forklift Jack
Safety guidelines emphasize adhering to load capacity limits, proper training, and regular equipment checks. Always follow operational procedures to minimize risks and ensure compliance with workplace safety regulations.
2.1 Operating Precautions
When operating a manual forklift jack, ensure the workspace is clear of obstacles and the floor is level to prevent accidents. Always wear appropriate safety gear, including gloves and safety shoes, to protect against injury. Check that the load is stable and evenly balanced on the forks before lifting. Never exceed the maximum load capacity specified by the manufacturer, as overloading can lead to equipment failure. Use smooth, controlled movements when lifting or lowering loads to avoid sudden jolts. Keep hands and fingers away from moving parts to prevent crushing injuries. Ensure proper visibility and maintain a safe distance from other personnel or equipment in the area. Additionally, never leave a loaded jack unattended, as this can pose a significant safety hazard. Always follow the manufacturer’s instructions for operation to ensure safe and effective use.
2.2 Importance of Load Capacity
The load capacity of a manual forklift jack is a critical factor in ensuring safe and efficient operations. Exceeding the maximum load capacity can lead to equipment failure, accidents, or personal injury. Always verify the weight of the load before lifting and ensure it does not surpass the jack’s rated capacity. Overloading can compromise the structural integrity of the jack, leading to mechanical breakdowns and potential hazards. Adhering to the load capacity guidelines helps maintain operator safety and prolongs the lifespan of the equipment. Additionally, understanding the load capacity ensures that the jack is used appropriately for its intended purposes, preventing misuse and enhancing overall productivity in industrial or warehouse settings; Never ignore the specified limits, as they are designed to protect both the operator and the equipment. Proper load management is essential for reliable performance and workplace safety.
2.3 Pre-Operation Safety Checks
Before using a manual forklift jack, it is crucial to perform thorough pre-operation safety checks to ensure safe and reliable performance. Begin by inspecting the jack for any visible damage, such as cracks, dents, or worn-out components. Check the hydraulic fluid levels and ensure all moving parts are properly lubricated to prevent friction and wear. Verify that the load-bearing surfaces are clean and free from debris. Test the jack by lifting a small load to ensure smooth operation and stability. Always ensure the work area is clear of obstacles and the floor is level. Additionally, check the condition of the wheels or casters for proper mobility. Never proceed without confirming that the jack is in good working condition and adheres to the manufacturer’s guidelines. These checks help prevent accidents and ensure the jack functions efficiently. Regular inspections also extend the lifespan of the equipment.
How to Use a Manual Forklift Jack
A manual forklift jack is operated by positioning it under the load, pumping the handle to lift, and maneuvering using the wheels or handles provided. Efficiency and safety are ensured by proper technique and adherence to load capacity guidelines. Regular maintenance, such as lubricating moving parts and checking hydraulic systems, is essential for optimal performance. Always ensure the surrounding area is clear and stable to prevent accidents. Following the manufacturer’s instructions and performing pre-operation checks are vital for safe and effective use. This tool is indispensable in industrial and warehouse settings for handling heavy materials with precision and ease. Proper training and understanding of its mechanics enhance productivity and workplace safety.
3.1 Preparation Before Lifting
Before using a manual forklift jack, it is crucial to ensure the work area is clear of obstacles and the surface is stable and level. Always wear appropriate personal protective equipment, such as safety gloves and steel-toe boots, to minimize risks. Inspect the jack for any damage, such as hydraulic leaks or worn wheels, and ensure all components are functioning properly. Check the load’s weight and dimensions to confirm it does not exceed the jack’s load capacity. Position the jack correctly under the load, ensuring it is centered and stable. Review the manufacturer’s instructions for specific preparation steps, as different models may have unique requirements. Finally, ensure the surrounding area is clear of personnel and obstacles to prevent accidents during the lifting process. Proper preparation is essential for safe and efficient operation.
3.2 Step-by-Step Lifting Process
To safely operate a manual forklift jack, begin by positioning it under the load, ensuring the forks are centered and stable. Slowly pump the handle to raise the jack, maintaining control of the load at all times. Continue lifting until the load is clear of the ground or surface. Once lifted, secure the load using straps or supports to prevent shifting. Carefully move the load to the desired location, ensuring the path is clear of obstacles. When ready to lower, slowly release the hydraulic pressure or crank the handle downward, keeping the load balanced. Ensure the load is placed on a stable surface before disengaging the jack. Always maintain control throughout the process and never leave the load unattended while lifted; Proper technique ensures safety and efficiency.
3.3 Post-Operation Procedures
After lifting, carefully lower the load to a stable surface and ensure it is secure. Turn the release valve to slowly descend the jack, maintaining control throughout. Once the load is placed, fully lower the forks to the ground to prevent accidental movement. Inspect the area to ensure it is clear of obstacles and personnel. After use, clean the jack and check for any damage or wear. Lubricate moving parts as needed to maintain smooth operation. Store the manual forklift jack in a dry, secure location, away from direct sunlight and moisture. Always ensure the jack is fully lowered and stable when not in use. Regularly inspect hydraulic lines and other components for leaks or damage. Following these post-operation procedures ensures safety, extends equipment lifespan, and prevents potential hazards. Proper storage and maintenance are crucial for optimal performance.
Maintenance and Troubleshooting
Regular maintenance ensures the manual forklift jack operates safely and efficiently. Inspect hydraulic lines, lubricate moving parts, and replace worn components promptly. Addressing issues early prevents breakdowns and extends lifespan.
4.1 Routine Maintenance Tasks
Routine maintenance is crucial to ensure the manual forklift jack functions optimally and safely. Start by inspecting all hydraulic lines and seals for any signs of wear or leakage. Clean the jack thoroughly, paying attention to moving parts to prevent dust and debris buildup. Lubricate pivot points and other moving components regularly to reduce friction and wear. Check the load-bearing surfaces and ensure they are free from damage. Additionally, test the jack’s lifting capacity by applying a known load to verify its performance. Replace any worn or damaged parts immediately to prevent accidents. Keep a maintenance log to track inspections and repairs, ensuring compliance with safety standards. Regular upkeep not only extends the jack’s lifespan but also enhances workplace safety and efficiency.
4.2 Common Issues and Solutions
Common issues with manual forklift jacks often stem from improper maintenance or overloading. One frequent problem is hydraulic fluid leakage, which can lead to reduced lifting power. To address this, inspect the hydraulic seals and replace them if damaged. Another issue is the jack’s failure to lift the intended load, often due to exceeding its capacity. Always verify the load’s weight and ensure it does not surpass the jack’s rated limit. Corrosion of metal components can also hinder functionality; regular lubrication and rust-proofing are effective solutions. Additionally, worn-out wheels or casters may cause mobility issues, requiring prompt replacement. Addressing these problems promptly ensures safe and efficient operation, minimizing downtime and extending the jack’s service life. Proper troubleshooting and timely repairs are essential for maintaining reliability and performance.
The manual forklift jack is an indispensable tool in industrial and warehouse settings, offering reliable and efficient load handling. By adhering to safety guidelines, performing routine maintenance, and understanding proper usage techniques, users can maximize its functionality and longevity. Regular inspections and timely repairs are crucial to prevent operational issues and ensure workplace safety. With its versatility and durability, the manual forklift jack remains a vital asset for lifting tasks, providing cost-effective solutions for various applications. Proper training and adherence to best practices further enhance its effectiveness, making it a cornerstone of material handling operations. Always prioritize safety and maintenance to get the most out of this essential equipment.